Implementing a well-designed Planned Preventive Maintenance (PPM) strategy is essential for forecourt owners aiming to optimise operational performance, reduce unexpected downtime and control maintenance costs.
By focusing on proactive maintenance, forecourt operators can enhance the reliability and efficiency of their equipment, ultimately leading to cost savings and improved customer satisfaction.

Efficient Operation of Dispensers
Routine maintenance keeps dispensers operating smoothly, lessening the risk of breakdowns, minimising downtime and enhancing customer satisfaction by providing reliable service. Regular inspections and servicing keep equipment running efficiently and safely, reducing the likelihood of leaks and spills that could cause environmental harm and be deemed a criminal offence.
Dispenser faults caused by clogged filters, worn and damaged parts, corrosion and meter drift may result in costly callouts and loss of business. However, a comprehensive maintenance and service schedule can prevent the majority of dispenser failures by ensuring systems are routinely inspected and any potential issues are addressed early. With consistent care and part replacements, dispensers will last longer, reducing wear and tear and preventing premature ageing and failure. This delays the need for dispenser replacements, providing significant cost savings and supporting the lifecycle of dispensers and other forecourt equipment.
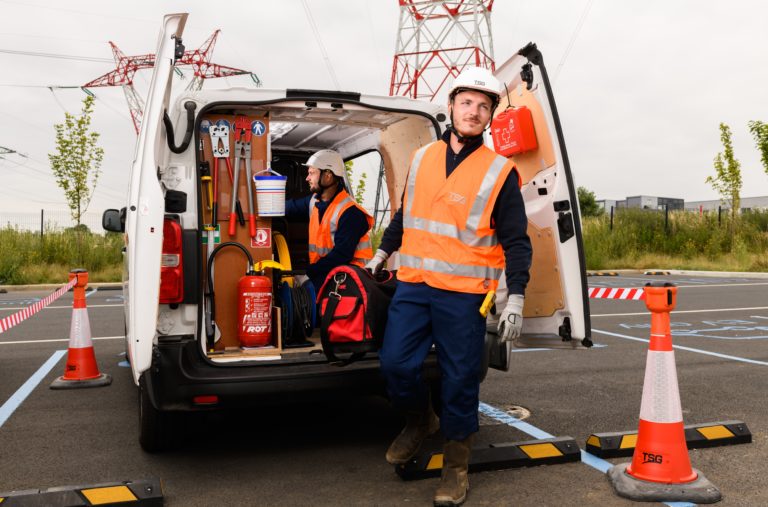
Cold weather can further impact forecourt equipment, making components brittle and more prone to damage. Additionally, condensation can form within the equipment, leading to potential freezing and blockages. Regular maintenance during colder months is crucial to mitigate these effects and keep equipment up and running.
Additionally, regular maintenance helps identify and address safety hazards, reducing the risk of accidents and injuries. PPM guarantees compliance with industry regulations and standards, avoiding potential fines and legal issues.
By integrating these practices, businesses can maintain a high level of operational efficiency and safety, ultimately providing customers with a more reliable and satisfactory experience.
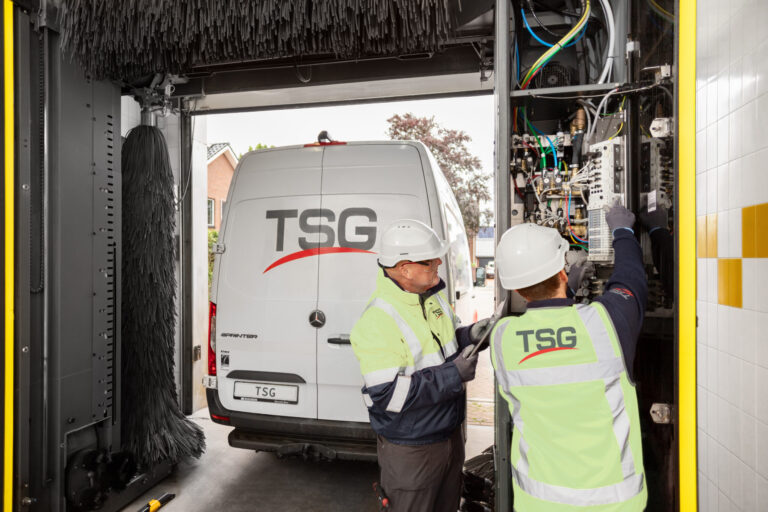
Vehicle Wash Systems
Proactive maintenance of vehicle wash systems helps prevent mechanical failures and safeguards consistent performance. Regular checks and servicing can extend the lifespan of the equipment and reduce repair costs. Customer retention hinges on customer satisfaction, which can be greatly enhanced by maintaining a clean and well-kept vehicle wash facility. Given the complexity of the equipment involved, it’s crucial to select a maintenance provider with extensive knowledge and the ability to deliver prompt, effective service.
In addition to professional service and maintenance programmes, site owners can follow general guidelines for routine daily checks. These include visual inspections of feed hoses, brushes, nozzles, drains, blowers, lights, water flow, detergent levels, pay stations (if applicable) and overall cleanliness. Performing regular vehicle test washes is also advisable to confirm brushes make full contact with the vehicle and soap is applied correctly.
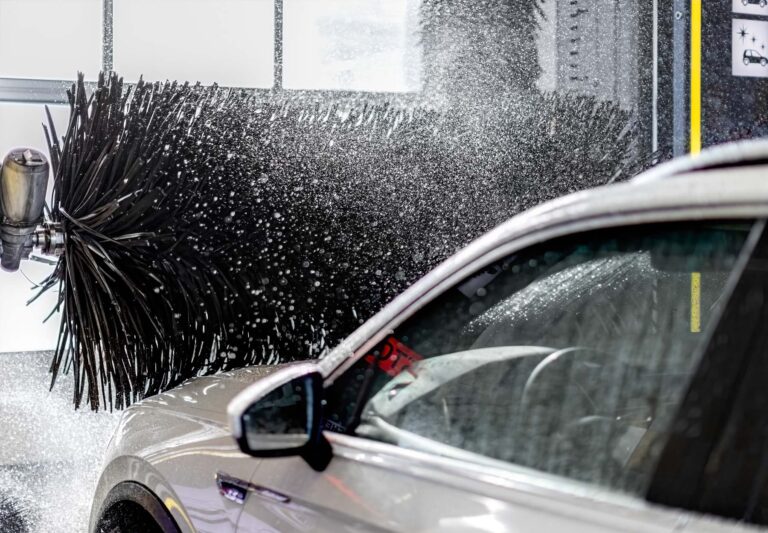
These simple checks can help identify potential problems early, allowing the wash manager to call for specialist assistance before issues escalate and cause operational downtime.
A busy vehicle wash facility, especially one that handles numerous dirty vehicles daily, can quickly lose its pristine appearance. Commercial wash operations that deal with large amounts of road grime, brake dust and bird droppings from fleet vehicles require regular cleaning to meet health and safety standards. Whether serving company drivers or the general public, site owners must uphold high cleanliness standards to achieve long-term success and sustainable profits for their business.
Spending just fifteen minutes with a jet wash each week (depending on usage) can restore the wash equipment to its former glory, helping to maintain customer retention and protect brand identity.
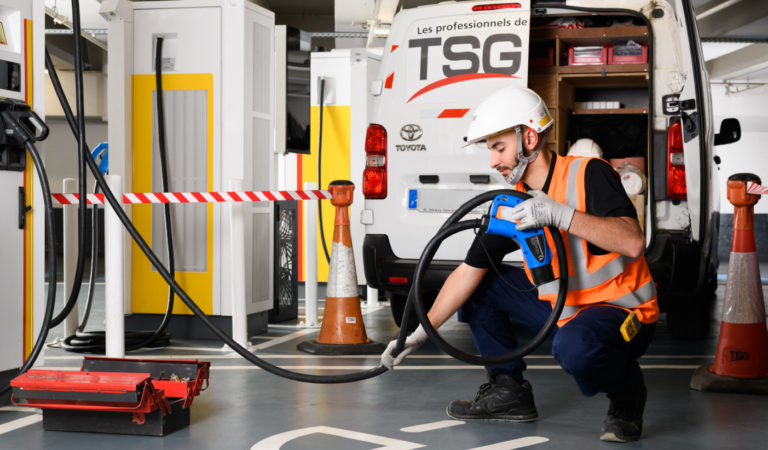
Maintaining Electric Charge Points
With the growing adoption of electric vehicles, maintaining charge points is crucial. Regular inspections and servicing can prevent malfunctions, providing EV drivers with access to reliable charging facilities. As an example, periodic testing of key components such as transformers, circuit breakers and cooling systems to confirm they are operating within optimal parameters. Furthermore, checking the efficient distribution of electrical loads across the chargers within the station will help to detect any irregularities in charging times, which could indicate issues such as low voltage or battery malfunctions.
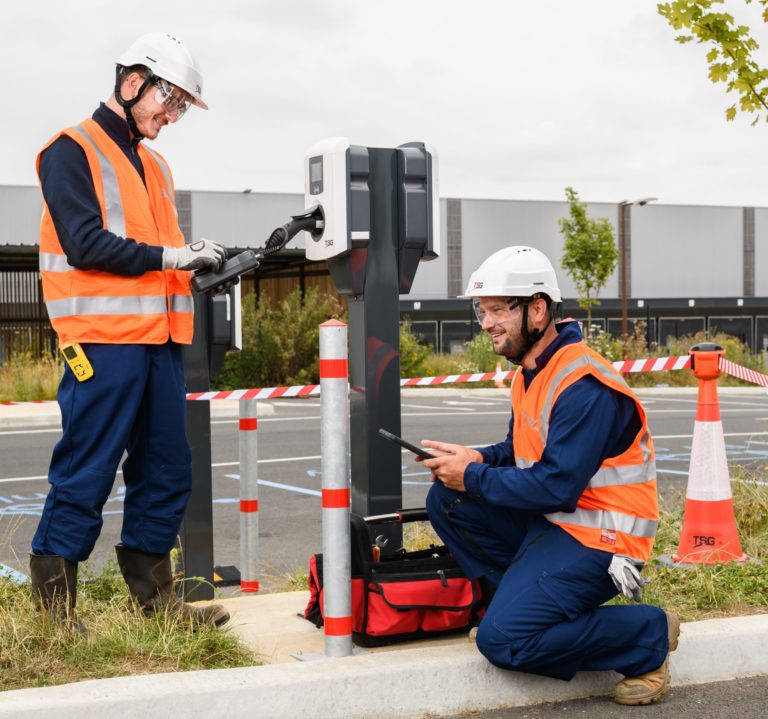
Implementing a PPM strategy for EV chargers helps them to operate reliably, preventing breakdowns and optimising uptime. This reduces repair costs and helps maintain the site’s reputation by complying with regulations and avoiding penalties. By minimising unexpected failures, PPM promotes a consistent recharging process and reduces the need for unplanned repairs. Regular maintenance also enhances safety by inspecting power supplies, connectors, and cables, which reduces risks for both staff and customers
Moreover, PPM extends the lifespan of EV chargers by identifying potential issues early, preventing untimely degradation and high replacement costs. It also fosters customer satisfaction by providing a seamless recharging process, clean facilities and reliable service, which boosts loyalty and competitiveness.
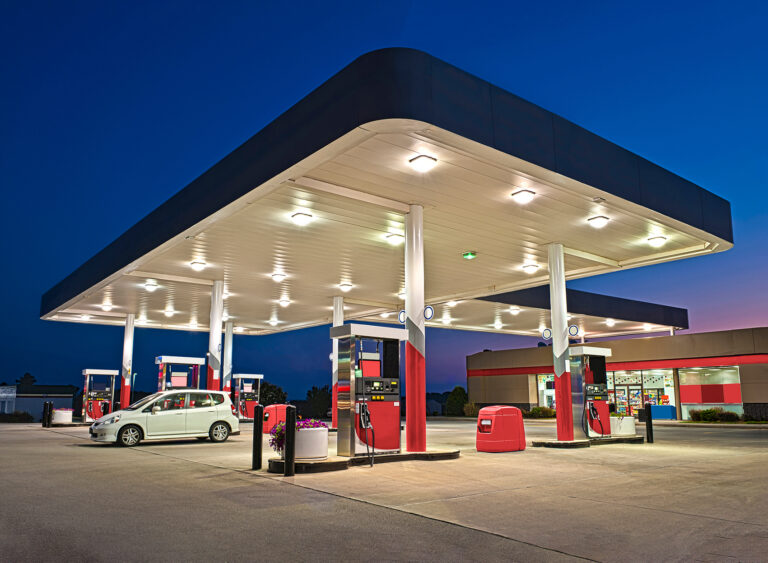
Maintaining Forecourt Appearance, Functionality and Safety
Preventive maintenance is essential for keeping forecourts looking good and functioning properly. Regular upkeep ensures that the forecourt remains clean, presentable and fully operational, which is vital for attracting and retaining customers. Well-maintained lighting is essential for safety and security on the forecourt. Regular maintenance can prevent outages and keep the forecourt well-lit, enhancing the overall customer experience.
Additionally, PPM is key for maintaining health and safety standards. Regular inspections and maintenance help identify and address potential hazards, reducing the risk of accidents and injuries on the forecourt.
Cost Savings and Operational Efficiency
PPM helps identify and fix minor issues before they become major problems, decreasing the necessity for expensive emergency repairs. Regular maintenance extends the lifespan of equipment, delaying the need for costly replacements. PPM serves as a safeguard against serious mechanical failures that can cause costly and time-consuming business disruptions. Proactive maintenance helps manage budgets more effectively by preventing emergency repairs and keeping equipment in optimal condition. This is particularly important for large fleet operations, where dispenser downtime can lead to considerable financial losses, making it crucial to maintain equipment to ensure smooth operations and minimise disruptions.
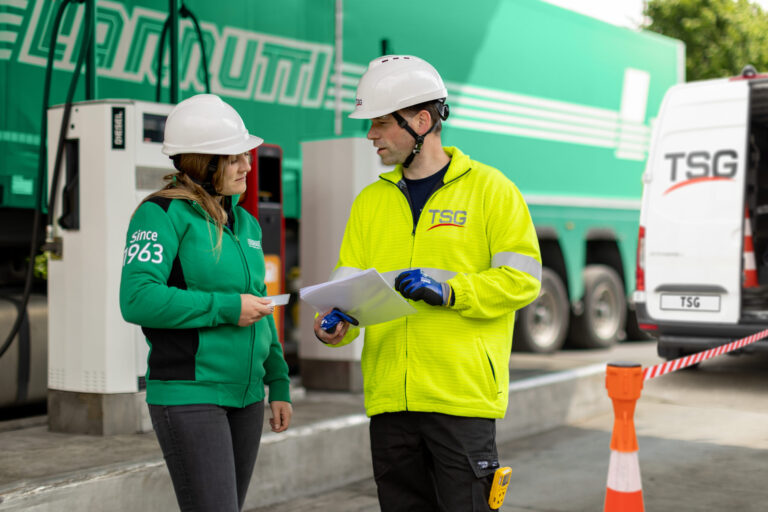
Avoiding Emergency Callout Fees and Preventing Problems
The fees for emergency repair services can be exorbitant and are often higher than routine maintenance visits. With preventive maintenance, dispensers are less likely to need emergency repairs, saving significant costs. PPM allows forecourt owners to be proactive rather than reactive, addressing issues before they cause damage, disruption or safety hazards. This preventative methodology avoids many costly reactive maintenance repairs altogether by anticipating potential problems before they arise.
By implementing a robust Planned Preventive Maintenance strategy, forecourt owners can ensure their operations run smoothly, efficiently and cost-effectively while enhancing safety and customer satisfaction.
TSG Ireland is here to help
At TSG Ireland, we understand the critical role effective preventative maintenance management plays in operating fuel retail networks. Therefore, we offer bespoke service and maintenance programs covering dispensers, wash solutions, lighting, signage, and EV charging stations throughout the year. We collaborate closely with our clients to create a service plan tailored to their unique needs.
Our team of specialists is always on hand to provide support, report faults, address issues or offer technical advice on forecourt equipment. For larger groups with more complex requirements, TSG can assign a dedicated key accounts manager who oversees their service and maintenance schedule and advises on system or equipment upgrades as needed.
By choosing a single trusted provider for all inspections and remedial work, site owners can maintain control over maintenance expenses and minimise the risk of unexpected callouts and unforeseen downtime.
Author: Cheryl Ashton